Emilio M. Morales, MSCE 1
Mark K. Morales MSc 2
Abstract: Testing of Fresh and hardened concrete has become routinary. This “routineness” has led to blind acceptance of the results without a real understanding of what the test results are saying and only “PASS”/“FAIL” conclusions are made on such results. However, the tests tell us what is happening or what is bound to happen if we do not heed the telltale indications that the tests are trying to convey. Oftentimes, lack of understanding of the failure or the causative mechanisms that bring about such failures are the least understood leading to wrong corrective responses or solutions. Problem identification has been said to be 80% of the solution process. Thus, there is a need to know the factors and significance of each test and the variables involved in the tests in order to arrive at solutions that directly address the problems. Most of the contents of this paper was obtained from literature more specifically from the work by Klieger et al on “ ASTM STP 160C – Significance of Tests and Properties of Concrete and Concrete-Making Materials”.and downloads from the Internet. Nevertheless, the authors hope that this paper could lead to a fuller understanding of the significance of the tests and what the test results are really telling us.
1.0 INTRODUCTION
Testing of Concrete both in the plastic and hardened states need to be carefully understood in order that adequate responses or proper corrective measures can be made to developing problems even before these develop.
Oftentimes, the test results and what they tell the end user remain as merely test results because of a lack of understanding on what these test results are really indicating to us and how they could best be used or interpreted to result in adequate and timely corrective measures to address the problem.
This paper references work by several authors from an ASTM Special Technical Publication ASTM STP 160C on the work by Klieger et al on “Significance of Tests and Properties of Concrete and Concrete-Making Materials”.and downloads from the Internet.
2.0 CONCRETE BASICS
Concrete is defined in the ASTM terminology relating to Concrete and Concrete Making Materials (C-125) as:
2.1 A composite material that consists essentially of a binding medium within which are embedded particles or fragments of aggregates.
2.2 In Hydraulic-cement concrete, “the binder is formed from a mixture of Hydraulic cement and water”.
2.3 Hydraulic cement is defined (ASTM C-219) as “a cement that sets and hardens by chemical interaction with water and that is capable of doing so under water”.
3.0 COMPONENT MATERIALS
3.1 Portland Cement
Portland Cement is the primary constituent of Portland cement Concrete.
It is defined as gray, powdery material that meets ASTM Standard C 150 and is composed primarily of tricalcium silicate, dicalcium silicate, tricalcium aluminate, and tetracalcium aluminoferrite. When combined with water, Portland Cement reacts with the water to form a paste, which then becomes rigid as the reaction between the cement and water progresses. 3]
Combined with the other components such as the inert fine and coarse aggregates and water, the Portland cement reacts (Hydrates) with water, initially forming a paste which within hours hardens to form the binding medium or cementitious matrix that holds the aggregates together.
3.2 Water
Next to Portland Cement, Water is an important ingredient. Water controls the strength and workability of the mix. The water reacts with the portland Cement in a process known as hydration to form a cementitious paste that hardens with time. The hydration reaction is a complex chemical reaction which physically alters the character and properties of the original Portland cement.
The water cement ratio is a good approximate indicator of the probable strength of the hardened mix. Its control is essential to a proper mix design which will address the job requirements.
Too much water in the mix will:
- Cause large shrinkages to occur if concrete is allowed to cure normally
- Result in low strengths
- Increased workability and flowability
There are real Reasons to use less water and these are to accomplish the following objectives:
- Increased strengths
- Lowered permeability
- Increased resistance to the effects of weather
- Better bonding with reinforcement
- Less volume change from wetting and drying
- Increased resistance to plastic shrinkage
If strength requirements as well as workability demands need to be met concurrently, addition of water while increasing workability can cause a retrogressive effect on the strength and increases shrinkage potential and should thus be avoided. Reduction of water in the mix would increase strength but may make the Concrete unworkable.
An alternative would be to consider the use of superplasticizers which dramatically enhances the workability and flowability of concrete while reducing the water demand and thus results in a concrete mix that will address the requirements of the project for strength and workability.
3.2.1 Water/Cement Ratio
The water/cement ratio is the weight of the total amount of water relative to the weight of the total amount of cement used per cubic meter of concrete. In simple terms, the lower the water/cement ratio or the less water used for a certain weight of paortland Cement in the mix, the better the concrete. This is true to a point. Enough water is needed to be able to place and consolidate the concrete as well as achieve complete hydration reaction.
The binding quality of the cement/water paste is due to the chemical reaction achieved when water is mixed with cement.
This reaction is called hydration. Very little water is needed for hydration. In fact, most concrete would look like a pile of rocks and be unworkable if the only water added was to hydrate the cement. Most of the water in concrete is “water of convenience” to help ease the task of placing concrete.
The more water added to concrete the thinner the paste. The thinner the paste, the less strength in the hardened concrete. The Portland Cement Association suggests using no more water than is absolutely necessary to make the concrete plastic and workable.
The graph below shows the effect of the Water Cement Ratio on the the Compressive Strength of Normal Weight Type I Portland Cement concrete at varying times based on tests on American Portland Cement Concrete. 4
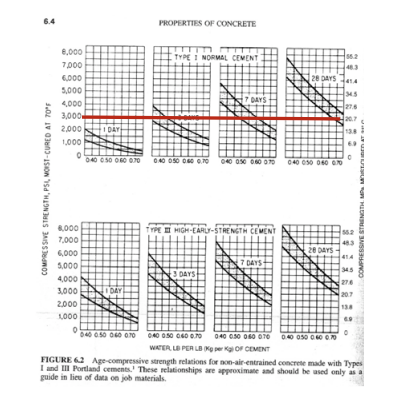
3.2.2 Water in Aggregates
Water in aggregates may or may not contribute to the hydration water depending on the condition of the moisture in the aggregates.
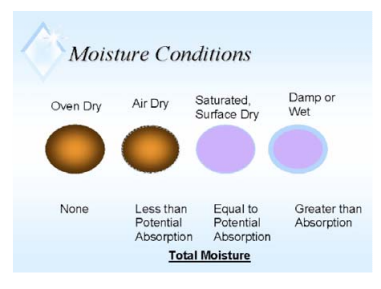
Water in the aggregates may also increase the available water as to increase the water cement ratio.
Thus, tests to determine the Moisture content of the aggregates is necessary for mix design purposes. The condition of the aggregates during the moisture content determination is also important as it determines whether the water is available as free water that could increase the water content of the mix or not at all. By the same token, it is necessary to determine the absorption capacity of the aggregates to determine whether hydration water will be reduced by absorption of the aggregates. Essentially, the absorbed water is not available to react with the cement as hydration water. Knowing the absorbed water will allow us to compensate for mix water that is “robbed” by aggregate absorption.
Normally aggregates are tested for absorption by using “Saturated Surface Dry Condition” as it is a measure of the potential absorption when moisture content under SSD is determined by Oven drying. the moisture content determined is then used to determine the absorption loss.
3.3 Air Content
Air content measurement is important particularly for non air entrained concrete because unexpected increases in air content can have a retrogressive effect on compressive and flexural strengths. The entrapped air bubbles displaces the cement matrix thus reducing the strength to some extent.
In tropical climates, air entrainment would normally only be prescribed for marine exposures for increased resistance to water permeability but more and more, this is being replaced by fly ash to provide a denser less permeable mix. However, even in the country, air entrainment for protection of the concrete (and eventually the rebar from corrosion) is done by using Fly Ash to promote a denser packing with minimum of voids in the concrete. The microfine fly ash fills these voids while at the same time increasing mobility and allowing for strength increases although in a much more delayed setting time.
3.4 Fine & Coarse Aggregates
3.4.1 Gradation Tests
Test of fine and coarse aggregates for grain size distribution is known as a Gradation test.
Grading is the particle distribution of granular materials among various sizes. This is usually expressed in terms of cumulative percentages larger or smaller than each of a series of sizes of standard sieves.
Grading and particle size distribution affects the overall performance of concrete as follows:
- Determines the relative aggregate proportions
- Determines the cement and water content
- Affects Workability
- Durability
- Porosity
- Porosity
- Shrinkage
The well graded the particles, the more economical is the mix. a well graded aggregate means that all the grain sizes are represented. This allows for economical, denser concrete mixes with increased strength.
Variations in grading from batch to batch can affect the uniformity of concrete.
Generally, aggregates which do not contain a large deficiency or excess of any particular size and give a smooth gradation curve, within the prescribed gradation will produce a satisfactory mix.
Providing a well graded gradation (where all prescribed particle sizes are present) will reduce the total volume of voids which otherwise will be occupied by the cement paste.
An air meter is normally used for measuring air content.
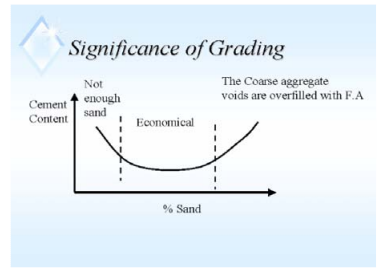
Fig 3.4.1.1 Cement Content vs % Sand Content illustrating the Significance of Sand Content to the
overall economy of the Mix expressed in terms of Cement Content demand
The Chart above shows that control of Sand content to within the prescribed guidelines will result in an economical mix. Too little sand would result in a very harsh mix and would require cement to be used as voids filler. Too much sand captures the cement paste to coat the individual grains resulting in increased cement demand.
For fine and coarse aggregates the fineness modulus (FM) is defined by ASTM C-125. The fineness modulus is obtained by adding the cumulative percentages retained (by weight) on each of the specified sieve sizes and dividing the sum by 100.
The higher the FM, the coarser is the aggregate.
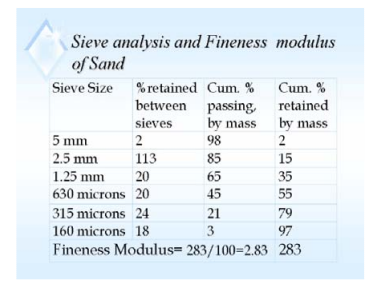
FM is important in estimating the proportions of fine and coarse aggregate.
3.4.2 Coarse Aggregates
The strength of aggregates, and hence its influence on the concrete, is primarily dependent on its mineralogy.
Beyond this, a smaller sized aggregate may have strength advantages in that internal weak planes may be less likely to exist or would be smaller and discontinuous.
The bond between mortar and coarse aggregates will be stronger for smaller aggregates.
A rough angular surface such as in crushed aggregates will increase the bond strengths.
As the maximum size of aggregate is increased for a given slump, the water and cement content per cubic meter of concrete are decreased.
The larger the coarse aggregate proportion is in the total mix, the lesser is the cement needed due to the lesser surface area compared to smaller aggregates. However, workability is affected and the mix becomes harsher with increasing aggregate size.
Flat elongated and angular shapes require more water to produce workable concrete. Hence, cement demand is increased to maintain the same WC ratio.
The larger the aggregate size, the lesser is the cement demand.
For coarse aggregates, the larger size materials tend to affect the strength of concrete particularly if the aggregates have weakened planes or discontinuities.
Gap graded aggregates may sometimes be used because of deficiency in coarse aggregate sizes within a certain sieve series. This would still be acceptable provided the percentage of fine aggregates is controlled. Gap graded mixes can produce a harsher mix but adequate vibration may address the problem.
Segregation is a problem in gap grading and therefore over vibration is to be avoided and the slump limited from 0 to 3 inches.
3.4.3 Fine Aggregates
Sand is primarily a filler for the voids in concrete.
Increasing the proportion of sand in the total mix increases cement demand because of the relatively very large surface area that needs to be coated by cement paste.
Flowability and mobility of concrete is enhanced with larger sand proportions but increases cement demand.
Flat elongated and angular shaped sands such as products from crushed sand, also require more water to produce workable concrete. Hence, cement demand is increased to maintain the same WC Ratio.
Generally, the gradation for fine aggregates given by ASTM C-33 would be adequate. However, it would be preferable to limit the % passing for the two smallest sieve sizes (#50 and #100 to 15% and 3% or more respectively. This would depend on workability during placement. The higher the fines content the more workable is the concrete but also increases cement demand.
4.0 FRESH CONCRETE
4.1 SLUMP TEST
The slump test is a measure of the workability of fresh concrete. It should NOT be used for predicting strength even in an approximate way.
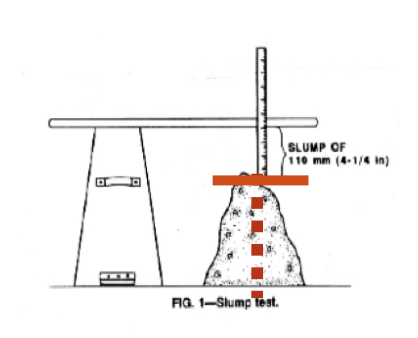
4.1.1 Additional Information from the Slump Test
More information can be obtained from the Concluded Slump Tests as follows:
- After removing the slump cone and measuring the slump, the concrete is tapped on the side with the tamping rod.
- Two concretes with the same slump may behave differently as follows:
- One may fall apart after tapping which indicates that it is a harsh mix with a minimum of fines. This may have sufficient workability ONLY for placement in pavements or Mass concrete.
- Another may be very cohesive with surplus of WORKABILITY, this may be required for more difficult placement condition
4.2 The Schmidt Rebound Hammer
The rebound hammer is an impact device that indicates relative and approximate concrete strength QUALITATIVELY through the rebound of the probe which has been calibrated against concrete strengths.
It is useful in determining or locating weaker or stronger concrete qualitatively and in a relative sense or for locating areas with discontinuities and honeycombs.
It is not an accurate device even when calibrated against concrete cores extracted in the area and is not intended to replace the compression test. It should NOT be used as a basis for acceptance or non-acceptance of a particular pour.
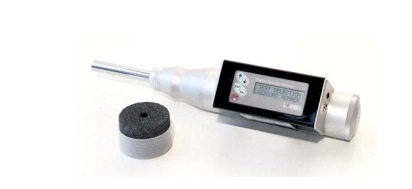
The device when used properly could give useful indications such as to where weaker vs Stronger concrete is present but only in a relative sense.
A lot of consultants think that it is an accurate and absolute determinant of Concrete compressive strength which it is not. Dependence on this as the sole reference and basis for rejection is unwarranted, unsound and NOT VALID.
4.3 Test on Concrete Core sample
Whenever the strength of hardened concrete is put to doubt, destructive testing in the form of testing concrete core samples uniaxially in accordance with ASTM C-42 is performed on the area where the questionable concrete has been laid. Coring is done using Diamond Coring bits that are thin walled. The core diameter should be no smaller than three times (3x) the size of the maximum nominal size of coarse aggregate.
Where possible, the length of the core should be at least twice the diameter (2X) of the core but other height to diameter ratios are permissible to a certain extent and corresponding correction factors are applied to the test results to compensate for the slenderness of the core sample. Reinforcing steel should not be included in the cores to be tested. If rebars do exist, the cores would have to be discarded and replaced.
When cores are taken for the purpose of strength determination, at least three cores should be taken at each location. The strength of the concrete as cored is expected to be lower than the design strength to take into account disturbance and damage effects during the sampling and testing of the cores. Values approaching 0.85 of the design concrete strength f’c or higher would be generally acceptable. 5 ]
4.4 Concrete Compression Test ASTM C-39
A concrete test as technically defined should consist of tests on at least two standard cylinders taken from the same batch or pour.
4.4.1 ACI Requirements for Compressive Strength Test
For a strength test, at least two standard test specimens shall be made from a composite sample obtained as required in Section 16. A test shall be the average of the strengths of the specimens tested at the age specified in 4.1.1.1 or 4.4.1.1 (Note 19). If a specimen shows definite evidence other than low strength, of improper sampling, molding, handling, curing, or testing, it shall be discarded and the strength of the remaining cylinder shall then be considered the test result.
To conform to the requirements of this specification, strength tests representing each class of concrete must meet the following two requirements mutually inclusive(Note 20):
The average of any three consecutive strength tests shall be equal to, or greater than, the specified strength, f’c, and No individual strength test shall be more than 500 psi [3.5 MPa] below the specified strength, f’c.
4.4.2 Failure Mechanism
Concrete failure in the compression test or in service is a result of the development of microcracking through the specimen to the point where it can no longer resist any further load.
The crack propagates through the weakest link whether it is through the aggregates or the cement matrix or both.
For ultra high strength concrete aggregate strength becomes critical and it would be better to have smaller sized aggregates so that internal weaknesses in the aggregates would not be significant as a crack initiator. Also, the use of small sized aggregates increases the aggregate interlock and increases the chances for Crack Arrest.
For normal strength concrete, failure normally propagates through the cement matrix unless internal planes of weakness in the aggregates give in more readily but the random distribution of these would arrest such crack propagation in the normally stronger aggregates.
In the compression test, because of scale effects, the planeness, perpendicularity and surface imperfections critically influence the results.
4.4.3 Factors Affecting Compressive Strength
Retempering of the mix with water in the concrete can cause a decrease in the mortar strength due to uneven dispersion of the retempering water which leads to pockets of mortar having a high water cement ratio.
If concrete is allowed to dry rapidly, the available moisture for hydration reaction will be reduced and hydration ceases.
A smaller sized aggregate may have strength advantages in that the internal weak planes may be less likely to exist.
The bond between the mortar and coarse aggregate particles will be stronger for smaller sized aggregates which have a higher curvature.
When concrete bleeds, the bleed water is often trapped beneath the coarse aggregate thus weakening the bond within the interfacial zone and allowing for weaker stress paths for cracks to initiate. Excessive bleeding will produce a high water cement ratio at the top portion leading to weakened wearing surfaces and dusting.
4.4.4 Break Patterns
Surface imperfections in the sample or the test platform can cause uneven break patterns which signal lower strength results normally.
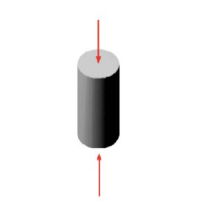
4.4.5 Factors Affecting the Compressive Strength Test Results:
Specimen geometry
Size
End conditions of loading apparatus
Rigidity of Test Equipment
Rate of load application
Specimen moisture conditions
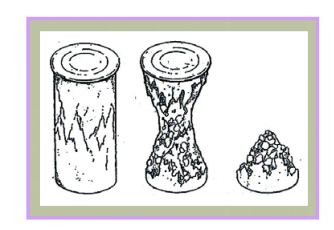
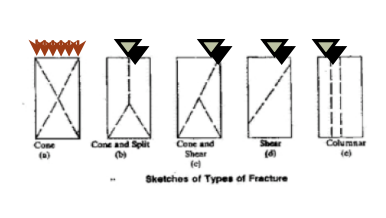
The purpose of specifying end condition requirements of planeness and perpendicularity is to achieve a uniform transfer of load to the test specimen.
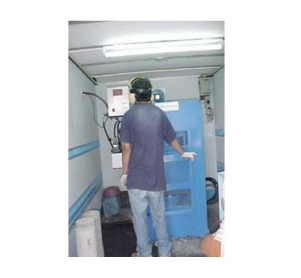
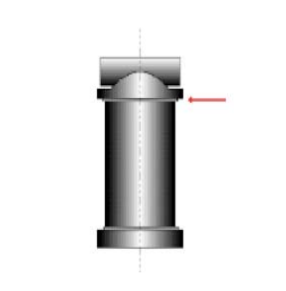

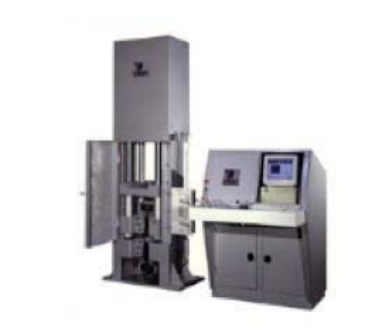
Non-conforming specimens generally cause lower strength test results and the degree of strength reduction increases for higher strength concrete.
4.4.6 Specimen Size and Aspect Ratio
The ASTM Standard test specimen is a 6” Diameter x 12” high cylinder.
Compressive strength generally varies inversely with increasing cylinder size with the 6” dia cylinder as the reference size.
The ratio of specimen diameter to max aggregate should be 3:1, the accuracy of the strength test results decreases as the diameter to aggregate ratio decreases.
The L:D (aspect ratio) requirements is 2. The strength increases with decreasing L/D ratio due to end restraint. However, correction factors are allowed.
4.4.7 Requirements of Testing Machine Properties
The Test Equipment used for the Compression test :
- Must be capable of smooth and continuous load application.
- Must have accurate load sensing and load indication.
- Must have two bearing blocks one fixed and the other spherically seated both satisfying planeness and rigidity requirements.
- Distortion of testing machine or of the bearing plates due to inadequate rigidity can cause strength reductions therefore, adequate rigidity needs to be assured.
4.4.8 Rate of Loading
ASTM C-39 requires that the loading rate for hydraulically operated test frames be controlled to within 20 to 50 PSI or about 500 Lbs per second. Other than making the test procedure follow consistent rates of loading and thus remove this as a variable effect on Concrete Strength, there are other reasons for prescribing a constant rate of loading.
The apparent strength of the concrete increases with increasing loading rate and therefore the loading rate must conform to the required standard to produce consistent and accurate results.
Higher strength concrete are more affected by the loading rate.
This dependence on loading rate has been found out to be due to the Mechanism of creep and Microcracking.
Thus, it has also been found out that when subjected to a sustained load of 75% its ultimate strength, concrete will eventually fail without any further load increases.
4.5 Concrete Flexural Strength
4.5.1 Factors Affecting Flexural Strength Test Results
Specimen Size
Preparation
Moisture Condition
Curing
Where the beam has been molded or sawed to size
Aggregate Size
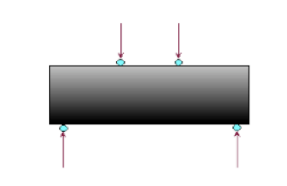
5.0 CONCRETE SHRINKAGE
Concrete shrinkage is primarily due to rapid and uneven loss of water. Therefore, improper curing of Freshly poured concrete and control of environmental factors plays a key roll in shrinkage control.
Drying Shrinkage increases with increasing water content. Therefore control of mixing water to that required only for complete hydration and desired adequate flowability is important. In case such conditions can not be met, it would be better to achieve these requirements by using water reducing plasticizers rather than by addition of more water.
Although control of total water in the mix is the primary objective to control shrinkage Cracking, other factors contribute to the overall shrinkage cracking as the following Equation would suggest.
Shrinkage cracking can be quantified or predicted based on ACI 209R-92 procedures as given in the following formula below. What is significant to note in this Formula is the contribution of other factors to the overall shrinkage magnitude which are controllable and thus points the way to the reduction of Shrinkage effects.
Prediction of Actual Shrinkage Values based on ACI 209R-92
Concrete shrinks due to moisture loss. However, the actual magnitude of ultimate shrinkage is dependent on a lot of factors as contained in ACI 209R-92.
These factors are:
- Relative Humidity
- Minimum Thickness
- Cement Content
- Slump
- Air Content
- Fines Content
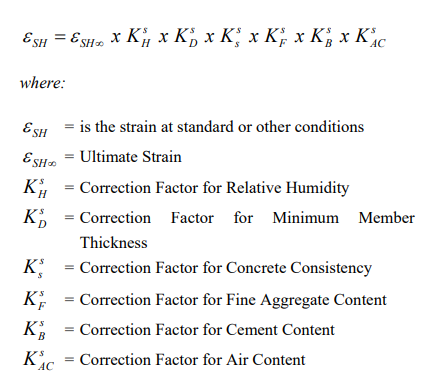
The parameter SH is obtained from the Chart below which is dependent on the Total Water Content of the mix when laid. The chart for obtaining the above variables are given in the Appendix of this paper.
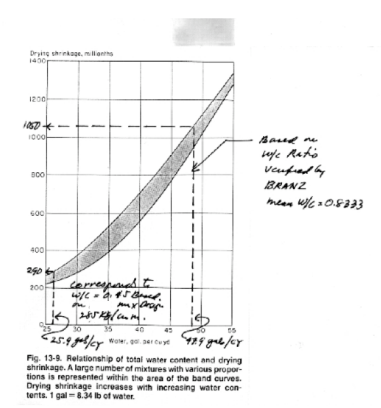
6.0 BLEED EFFECTS
Although not related to shrinkage, bleeding is A related surface defect that is controllable. Bleeding occurs when over-troweling happens which works up more water to the surface.
The increased water at the surface results in higher W/C which causes a low strength layer that can delaminate and cause dusting or powdering.
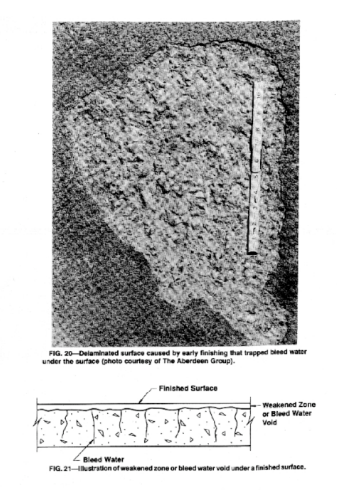
7.0 CONCLUSIONS
This paper has identified the various Factors affecting tests on fresh and hardened concrete and their significance in influencing test results.
A complete understanding of these Factors can definitely reduce uncertainties in determining the cause/s of “Failed test Resultsˆ and eliminate costly Guesswork and often times solutions that do not address the problem.
The Authors hope that recognition of the various factors that influence the test results could lead to a more positive and responsive solution to problems brought about by the test results.
REFERENCES
Klieger, Paul and Lamond, Joseph F. “Significance of Tests and Properties of Concrete and Concrete- Making Materials”. ASTM STP 160C.
ACI 209 R -92 METHOD OF SHRINKAGE PREDICTION.
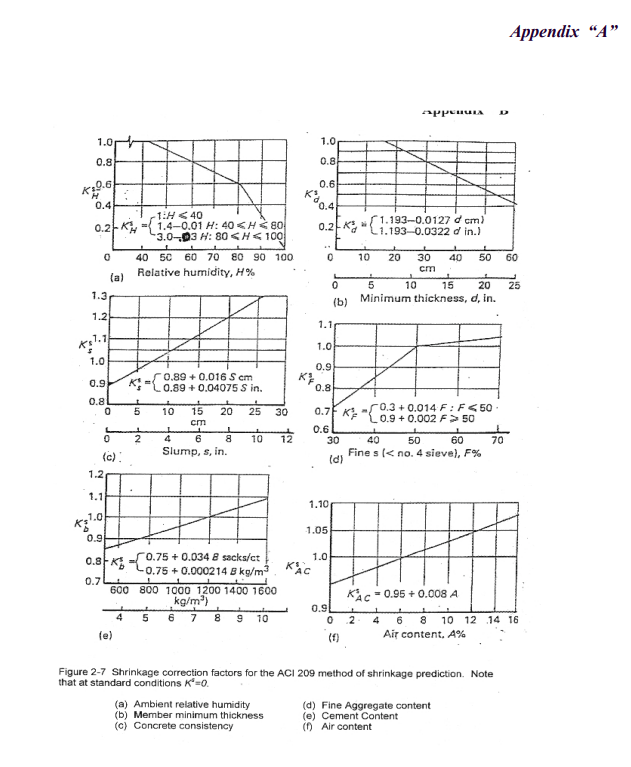
1 Emilio M. Morales, MSCE took his Master of Science in Civil Engineering at Carnegie-Mellon University, Pittsburgh, PA. USA in 1980. He was employed as a Geotechnical Engineer at D’Appolonia Consulting Engineers. Currently, he is the Principal of EM²A Partners & Co. and concurrently serves as President for IGS Philippines, Chairman for the PICE Geotechnical Specialty Committee. He has been elevated to PhD Candidacy at the Asian Institute of Technology, Bangkok,
2 Mark K. Morales, MSc took his Master of Science in Civil Engineering at University of California – Berkeley, USA in 2004. He is the Technical Manager of Philippine Geoanalytics, Inc. and President of PGA Earth Structures Solutions
3 www.ces.clemson.edu/arts/glossary.html
4 NOTE: Slightly Lower results are obtained for philippine Cements due to lower cube compressive strengths but the chart is indicative of the relationship between Concrete Strength and W/C
5 ACI 437R-16 “Strength Evaluation of Concrete Buildings” Excerpts
Download Significance of Tests on Fresh & Hardened Concrete