Concrete compression testing is a fundamental test procedure for civil engineering and construction quality control and assurance used to evaluate the strength and quality of concrete. This procedure involves applying a compressive load to a cylindrical specimen until failure occurs. It is conducted in a controlled laboratory setting adhering to specific standards and protocols.
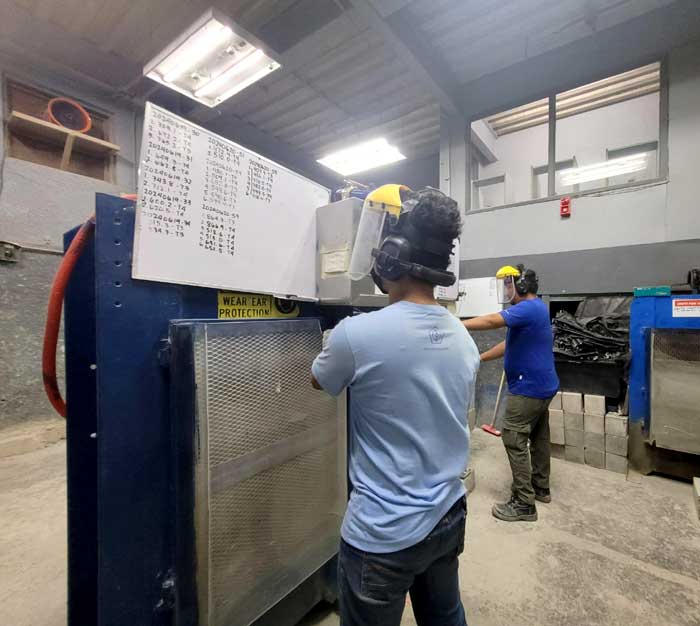
The results of concrete compression testing is focal in assessing the load-carrying capacity and structural performance of concrete in various construction applications, including buildings, bridges, pavements, and infrastructure projects. Structural and field engineers rely on these test outcomes to verify that the concrete meets the necessary strength and safety requirements.
Concrete testing generally follows a procedure that involves the following:
Sample Preparation:
Concrete specimens are cast in standardized molds, typically cylinders with a diameter of 150 mm (6 inches) and a height of 300 mm (12 inches). The specimens undergo careful compaction and curing under controlled conditions to achieve the desired strength.
Testing Apparatus:
The prepared concrete specimens are placed in a compression testing machine, which applies a progressively increasing load to the specimen. Equipped with load cells and a digital display, the machine accurately measures the applied force.
Loading Procedure:
The test commences with a pre-loading phase, during which a small load is applied to eliminate any irregularities or gaps between the specimen and the testing machine. Subsequently, the main loading phase ensues, gradually increasing the load at a specified rate until the concrete sample reaches failure.
Failure Criteria:
Failure of the concrete specimen is determined when it can no longer withstand the increasing load, causing the measured resistance to decrease. The maximum load the sample sustained before failure occurs is recorded as the compressive strength of the concrete.