Innovative Foundation Solutions Save the Day
Author: EMILIO M. MORALES, MSCE (Principal)
Organization: EM2A Partners & Co.
Address: QUEZON CITY, PHILIPPINES
ABSTRACT
Foundation problems abound and sometimes solutions to various foundation problems could result in costly procedures or measures in order to remedy the problem. Introduction of Innovative Solutions to problems in Foundations together with a clear understanding of the problem and application of Innovative Technologies result in cost effective solutions. Two case studies are presented in this paper to illustrate such solutions.
Key Words: Underpinning, Ground Improvement, Jet Grouting, Rammed Aggregate Piers, Geopier®, Settlement Ground Vibrations
INTRODUCTION
The subsurface soils being natural deposits tend to introduce unexpected variability in the subsoil that is not revealed by the soil exploration or during construction. This situation could lead to costly delays in the process. In addition, errors in construction of foundations could lead to serious problems that would require costly intervention.
This paper addresses the foregoing real world problems, which have been solved with the use of innovative foundation technologies.
Two (2) case studies are discussed to illustrate the measures and solutions employed to solve the problem.
CASE I – SETTLEMENT OF BORED PILE FOUNDATIONS
A pier supporting 60 m long span Precast concrete Box Girders for a light rail transit line crossing a river experienced significant settlement immediately upon placement of the Girders (Dead Load).
This initial settlement of 36mm caused concern and was continuing progressively until loading and other construction activities were halted. At that time, a total of 45.7mm maximum settlement has already resulted.
The erection subcontractor for the Precast Concrete Box Girder segments specified a short-term maximum settlement of 30mm and a total long-term maximum settlement of 45mm.
The initial settlements have actually exceeded these values and the Box Girders have to be relevelled by jacking in order to level the Girders. All construction activities were halted at this juncture and intermediate heavy steel supports were placed near the Pier support in case further settlements are experienced.
Our organization was engaged by the Contractor initially to undertake an investigation of the subsurface to determine the possible cause/s of the settlement which was very alarming considering that this particular Pier is supported by six (6) large diameter Bored Piles on a massive pile cap.
The following are the details of the Bored Pile foundation:
Number of Bored Pile N = 6
Diameter of Bored Pile D = 1500 mm
Length as installed L ] = Varies
Theoretical Allowable
Load bearing Capacity (MT) ]
CStatic = 515.46 MT/pile
CEqk = 799.69MT/pile
The design called for embedment into soft Bedrock of 1.0 to
2.0 meters depending on whether the Bored Pile embedded length is long or short (> or < 10.0 meters).
Two check Boreholes were drilled, one at the toe of the Pile
cap and another near the edge of the column close to the middle Bored Pile.
The check Borings (Fig. 1.0 below) indicated that the overburden soils are relatively poor to very poor beyond 7 meters as shown in the Soil Profile below for BH-1 and BH-2.
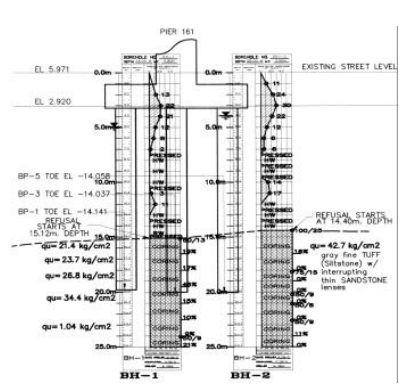
As can be seen, refusal was only encountered at a depth of 15.12 meters and 14.40 meters below existing Natural Ground Line.
A tabulation of the drilling results when matched against the installed depth is shown below:
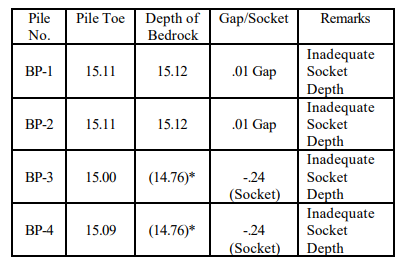

As can be seen from the above, two of the Bored Piles (BP-1 and BP-2) were literally resting on very soft clay and the rest were socketed only about 0.24 meters into the possibly highly weathered Soil/Bedrock Interface.
The RQD values below the soil bedrock interface showed relatively fair values of 19% and 16% respectively.
Bedrock Unconfined Compressive Strengths are about 20.0 kg/cm2 near the Bored Pile Tip characteristic of soft rock known as the Guadalupe Tuff Formation (GTF).
Thus, the heavily loaded Bored Piles were either resting on very soft clay or on relatively weathered Bedrock very near the Soil Bedrock interface without adequate socketing.
The remaining gap is about 10mm after the recorded settlements. Thus, it was possible that the clays have been squeezed out at some locations resulting in the Bored Piles resting partly on the Bedrock and partly on very soft clay.
This is the primary cause of the relatively large settlement that was experienced at this particular Pier location.
Geology of the Site
The site across the San Juan River in San Juan, Metro Manila is generally underlain by the Guadalupe Tuff Formation (GTF), a massive suite of soft Tuffaceous Volcanic rocks.
The Pier Foundations that settled supported the Eastern end of the 60 m long girders spanning the river.
Overburden soils are relatively poor to very poor below 7 meters and consist of clays and silts down to about 15.0 meters and sloping towards the San Juan River.
The thick and very poor overburden needed to be bypassed by Bored Piles to transfer the foundation loads to more competent rock.
What Caused the Settlement?
The Bored Piles were not adequately socketed as required and were partly resting on very week materials. It was possible that boulders and large cuttings were encountered which resulted in erroneous interpretation that the Bedrock level had been penetrated.
As stated earlier, the specification called for a minimum socket depth of 1.0m to 2.0m into bedrock. No clear or reasonable explanation could be given as to why the Bored Piles were installed short of the target depth. It can only be assumed that this was overlooked during the installation and the hole was not cleaned or inspected at all.
The Jet Grouting solution was finally selected because it offered a far better assurance of stability during seismic loadings. As shown in Fig. 3 the solution consisted of providing a Jet Grouted Wall around the footprint of the Pile Cap and at several interior locations as shown in the plan.
This Jet Grouted Curtain Wall in Secant Pile arrangement would assure full assumption of the load from the Bored Piles while at the same time increasing resistance to sliding and overturning.
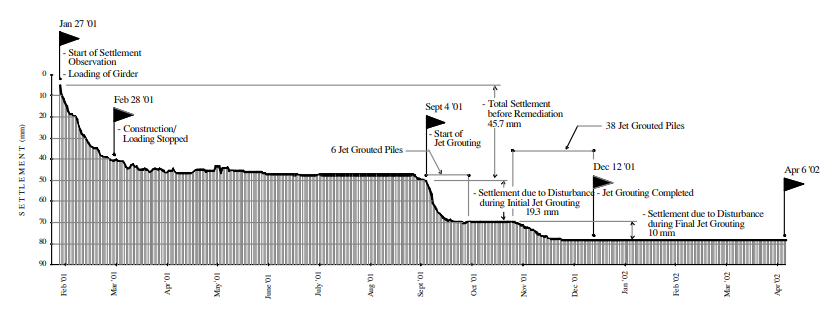
Remediation Measures
Immediately upon detection of on-going settlements, formal settlement monitoring and recording was started 27 January 2001. Because of continuing high rate of settlement, construction loading was halted on February 28, 2001. Heavy Structural Steel scaffolding was placed to support the Girders and Jacking releveled the Girders. Still settlements continued but at a reduced rate resulting in a total of 45.7mm settlement of the Pile Cap.
The ensuing check borings (Fig 1.0) verified that the Bored Pile tips were resting on very soft soils or on highly weathered bedrock.
Several remediation measures were discussed and these were narrowed down to two feasible technologies:
- Micropiles
- Jet Grouting (JGP)
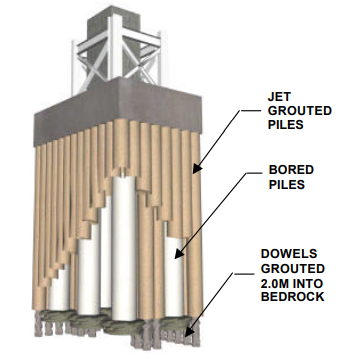
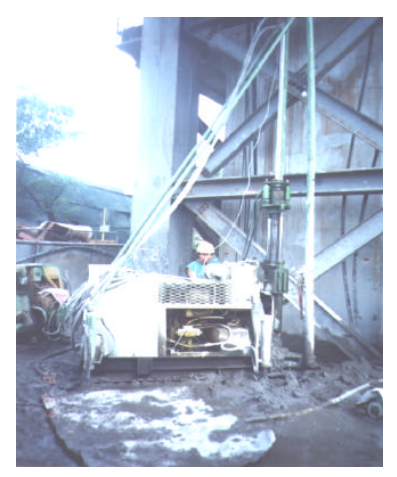

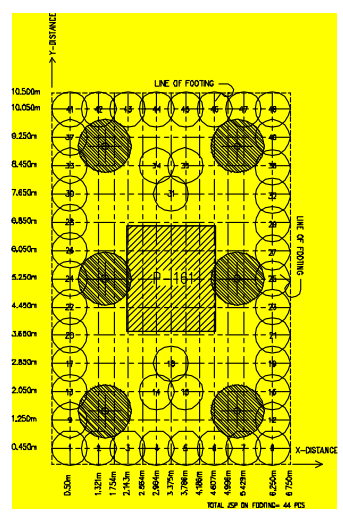
In addition, each of the Jet Grouted Piles were reinforced at the center by 25mm Ø rebars which were inserted by redrilling the Jet Grouted Piles (JGP) and extending 2.0 meters beyond the Soil/Bedrock interface into competent Bedrock. The drilled hole and dowel bar were subsequently regrouted effectively doweling each JGP into the Bedrock. Expansive admixture and higher strength mix was used to grout the rebar to the Pile Cap. This provided extra shear capacity over and above that provided at the Pile Cap/JGP Interface.
The settlement record for the project is shown in Fig. 3. The milestones are flagged. It can be seen that with the initial Jet Grouting, additional settlement of 19.3mm was experienced due to further disturbance of the weak soils near Bored Pile Tips, although care was exercised to reduce such disturbances to the minimum by initially drilling far from the Bored piles. The Girders had to be releveled again by Jacking.
The Jetting was halted to allow for the curing of the Soilcrete and also because questions were raised about the effectiveness of the technology given the additional settlements. After Field trials were done to verify the effective diameter of the JGP and the Guaranteed Compressive Strength it was shown that the Test Piles satisfied or even exceeded project requirements. Subsequently, Jet Grouting was restarted for the final Jet Grouting of 38 Piles on November 1, 2001. Only 10mm additional settlements were recorded. The Jet Grouting was completed on December 12, 2001.
Although the Jet Grouted Curtain wall would be more than adequate to support the total foundation loading, the Project consultants required that the existing Bored piles be redrilled at the center to allow for the insertion of Grouting equipment in order to grout the pile tip. This would ensure that once the “Soilcrete” has cured, the Bored pile tips would be resting on solidified ground. This was accomplished after the initial JGP installation and was done initially in areas where the JGP have substantially cured and attained full strength.
The solidification at the tip of the Bored pile is shown in the figure below:
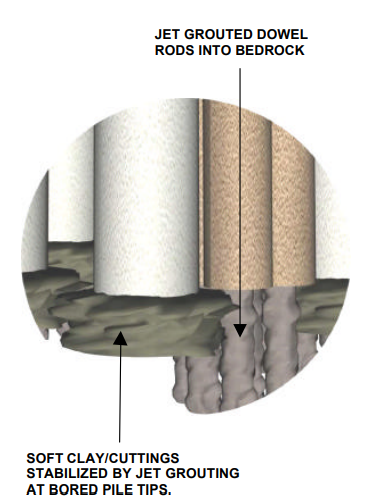
No further settlements have been recorded despite the placement of ballast and rail tracks as well as other hardware and the remediation was considered successful.
Lessons Learned
Careful monitoring of the Bored Pile installation is very important to ensure the integrity of the Bored Pile foundation including adequate and proper cleaning of the bottom from cuttings and degraded rock. It is also important to ensure that the specified socket depth is attained.
The innovative remediation process instituted successfully arrested the settlements and restored the Pier to full serviceability.
CASE 2 – WAREHOUSE CLUB ON VERY POOR SOILS
A 6,500 square meter retail warehouse was to be constructed on very poor swampland soils originally used as a precast concrete plant yard.
The original solution called for Driving of R.C. Precast Piles to support the warehouse including the Warehouse floor, as anticipated settlements would result in cracking of the heavily loaded floor. The suspended structural floor supports merchandise racking with a distributed load of about 450 psf. The levelness of the floors is critical for the safe operation of the medium reach forklifts used in the warehousing operations.
However, during the initial Test Pile driving, complaints were received from the neighborhood residents due to large vibrations experienced as well as damage due to cracking of walls in several houses.
The damage was due to soft ground amplification of the pile driving vibrations. Work had to be halted indefinitely until a substitute could be proposed. The only alternative was to use Bored Piles. In order to optimize and mobilize the full capacity of the Bored Piles, the Bored Piles would have to be deep and the loads concentrated onto a limited number of Bored Piles. This, in turn, required heavy structural framing systems consisting of Deep Girders and Beams to carry the heavily loaded Warehouse floor and transfer the loads to the Bored Piles. The resulting cost of the Bored Pile foundation and heavy floor framing system was estimated at P45.0 Million.
Value Engineering Alternative
Our company offered a value engineering alternative using Geopier® foundation. The proposed solution consisted of installation of about 1900 Geopier of 3.0 to 3.5 meter length supported on the very soft soils. The Geopier foundation system is a Rammed Aggregate Pier system using patented technology. Installation is done in the following sequence shown by the fig below:
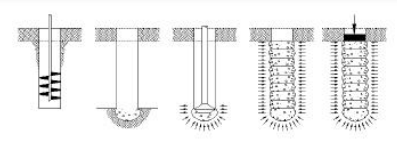
Due to the installation procedure, which consisted of ramming the aggregates using a patented beveled rammer, lateral prestraining and precompaction of the surrounding soils were realized. This prestraining and prestressing effect resulted in significant increases in lateral stresses around the Geopier perimeter resulting in very significant stress transfer by skin friction to the surrounding soils. Only very minimal residual stresses due to the loading were transferred to the Geopier tip thus resulting in large reduction in settlements of the Geopier.
The columns were supported on two or three 3.5 meter Geopier. Columns supporting Canopies requiring uplift resistance were supported on tension Geopier, which were reinforced with, rebars restrained near the Geopier tip by steel plates.
The suspended structural framing Support of the merchandise and warehouse floor was totally eliminated. In its place, a very innovative slab support system was substituted. The slab support system consists of a 1.0 meter thick Engineered Granular fill supported on Geopier at 3.0 meter on centers by arch action. The arch action transfers the entire load onto the Geopier elements. This enabled the floor slab to be designed as a conventional slab on Grade with reduced reinforcement and with very minimal settlements.
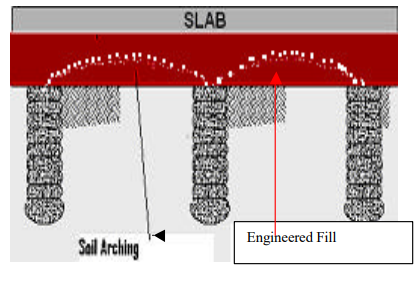
fill to transfer floor loads to Geopier by Soil arching.
This value engineering alternative was considered only after written guarantees secured by a USD 500,000 liability insurance was issued by our US Principals to limit the settlements to within 20mm.
However, this innovative solution presented several advantages to the owner as follows:
- Reduction in foundation installation time
- Reduction in overall construction time by elimination of a structural floor system.
- Significant cost reduction due to the high cost of Bored Piling as well as the integral structural floor framing system.
Furthermore, it was stipulated that we have to perform an actual Field Installation demonstration with the Village Association Officers in attendance in order to convince them regarding the minimal vibration and noise resulting from the installation and also to ensure that no damage will result from such activities.
This was successfully done and the contract was awarded to the company.
Modulus Load Test
As part of the execution, a Modulus load test was performed on a production Geopier in order to determine the settlement under the full service load. The Geopier Modulus test is similar to the setup used in a pile load test but the interpretation is different.
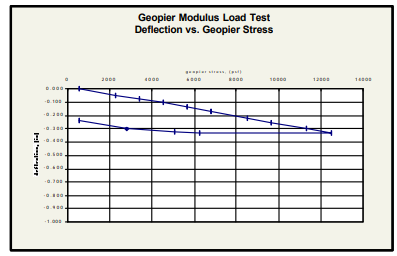
The Stiffness modulus values of installed Geopier elements are determined by full-scale modulus tests. The test is performed by applying pressure in gradual increments over the full cross-section area at the top of a Geopier element. The stiffness modulus value corresponding to 100% of the design stress applied to the top of the pier is determined based upon the load test results, and is typically expressed in English units as pci, and in metric units as MN/m3. The Geopier modulus load test is not a bearing capacity type test, such as a pile load test. Rather, it is a settlement test to determine a conservative value of pier stiffness. The Geopier foundation system design uses the stiffness modulus value measured at the point of maximum anticipated design stress; i.e., at 100% design top of Geopier stress (or at the maximum acceptable deflection) from the modulus load test results. Geopier modulus tests are normally performed to a top of Geopier stress equal to 1.5 times the maximum design stress. The purpose of applying load to more than the design stress is just to observe the Geopier element deformation characteristics at higher stress levels.
The results of the Modulus load test for this specific project is shown in Fig. 12 below:

As can be seen from the above a total of only 0.218mm settlement was obtained under full service load and that failure was not reached at 1.5 times the maximum service load. A residual settlement of only 0.231mm was left after unloading of the Modulus test.
The installation was done at the height of the Typhoon season but the project was completed on time.
As a result of this Value Engineering alternative, the construction time was shortened by two (2) months allowing for an earlier opening of the Warehouse club. This was because the heavy suspended floor was totally eliminated and the floor was designed as slabs resting on a compacted engineered fill instead. The engineered fill in turn is supported on Geopier spaced at 3.0 m on centers by arch action.
The construction sequence also was favorable to the General contractor as the GEOPIER procedure allowed immediate work to be undertaken immediately after a section has been completed. Critical time waiting for the curing of piling etc was totally eliminated. Compaction of the engineered fill was started at sections adjacent to Geopier installation activity without the possibility of disturbance to the engineered fill. Pouring of the concrete slab on grade immediately followed the completion of the engineered fill compaction. At any given time, concrete pouring was about two bays distant from any Geopier installation activity, thus vibrations are no longer a critical issue during the curing of the concrete.
This also resulted in a savings of about P 20 million over that of the cost of bored piling and suspended structural floor system.
The project was completed two months ahead of the original scheduled date of opening and the overall savings due to this value engineering solution was very significant.
Lessons Learned
Pile driving on very soft soils can cause amplification of harmful vibrations, which could damage adjacent structures. In addition, breakages of driven concrete piles during driving are possible due to the setup of tension waves from rapid pile driving. Costly suspended floor systems can be eliminated with the use of innovative solutions for load support.
Conclusions
The foregoing are but two of many available solutions to solve day-to-day Foundation problems innovatively. The two cases also illustrate what can go wrong in a project, which may require the use of new or innovative technologies to solve the problem effectively.
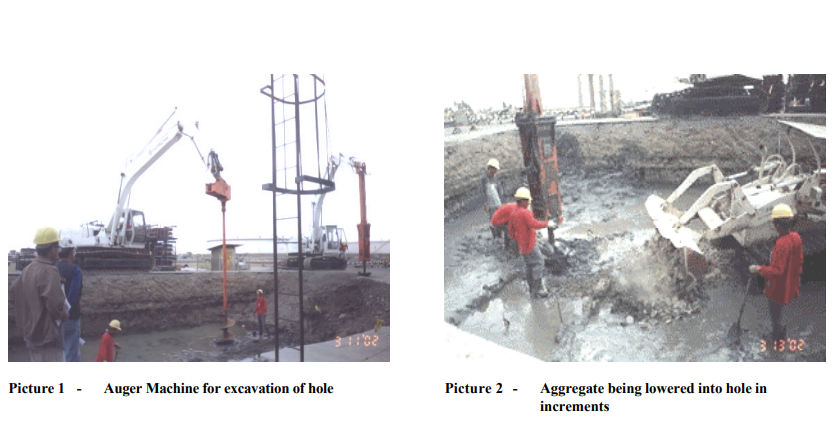
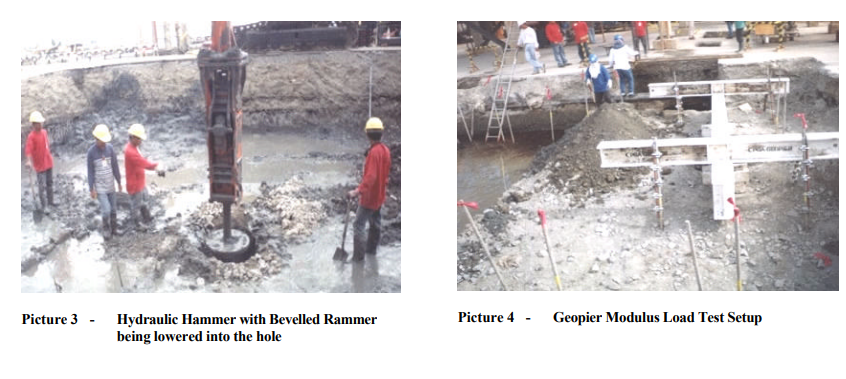
] Based on Piling Contractor’s Bored Piling record.
] From Capacity Calculation Sheets.